- Top
- Corporate Information
- Building Automation Solutions Business
Building Automation
Solutions Business
Reducing total costs and CO2 emissions from the standpoint of customers
Nihon Dengi provides solutions to various issues that arise in the course of maintaining buildings, factories, and other structures.
We help to tackle problems ranging from repairs and upgrading as part of preventive maintenance to ESCO (*1) proposals aimed at achieving energy savings over the medium to long term in response to various needs, such as extending the life of buildings, enhancing the added value of assets, and reducing LCC (*2).
- *1 ESCO is an abbreviation for “Energy Service COmpany,” i.e., a company that provides comprehensive energy saving-related services for factories and buildings and guarantees the results of the energy-saving measures implemented.
- *2 Life cycle cost (LCC) refers to the cost incurred over a building’s lifetime from its planning and design to demolition, with maintenance and management costs incurred after a building’s completion accounting for approximately 50% of this cost.
![Life Cycle Management Source: Building and Equipment Life Cycle Association (BELCA) [Running costs] Construction costs:25%, Maintenance costs (facility management, cleaning, security):15%, Repair and upgrading costs:11%, Operating costs (energy):21%, General and administrative costs:27%, Corporate design costs:1%](/en/company/img/fig-solution.png)
Reduction of running costs Cost Savings
Buildings incur significant running costs over their lifetime, including maintenance costs such as facility management and operating (energy) costs. Through our maintenance services, which involve regular visits to monitor the equipment’s utilization and operational status, we offer proposals to help customers reduce their running costs.
Acute awareness of the environment Eco-friendliness
Laws, regulations, and various efforts aimed at achieving a carbon-neutral society have gained traction in response to the issue of global warming. To tackle problems related to reducing energy use faced by customers, we leverage our engineering capabilities based on our extensive experience to assist customers by offering proposals for the renovation of building equipment and providing advice on the efficient operation of equipment.
Advanced facility services through remote monitoring Remote Maintenance
We utilize information technology to collect operating data automatically. Based on the data collected, we provide advanced preventive maintenance services where we analyze the utilization status of systems and diagnose any problems (condition-based maintenance).
Provision of maintenance services that focus on the present and future of buildings Flexibility
The usage environment of buildings, factories, and other structures varies from day to day as a result of changes in tenants, layout, manufacturing equipment, and other factors. We help to maintain an appropriate spatial environment over the medium to long term by providing services on a perennial basis.
Other businesses
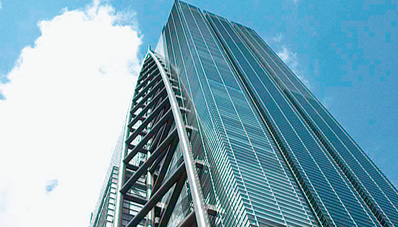
We provide new building systems by drawing on the extensive expertise we have accumulated.
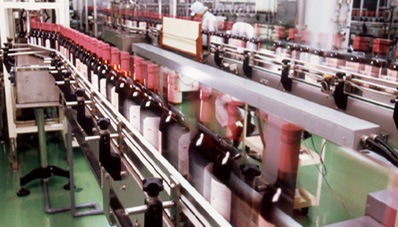
We address various needs ranging from productivity improvement to quality maintenance and environmental considerations.
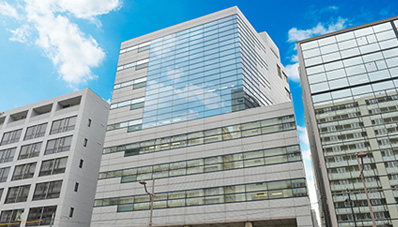
Our dedicated team of engineers is fully equipped to support the automation requirements of customers.
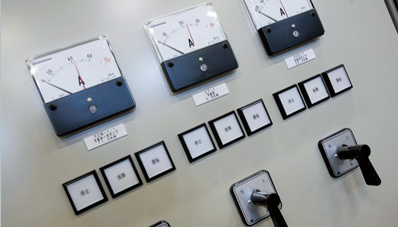
We manufacture control panels, monitor panels, power panels, etc., all of which play vital roles in automatic control, at our own factories.